Plastic Injection Heaters
Heaters for Plastic Injection
Heaters used in plastic injection processes serve the function of heating equipment used to melt and shape plastic materials. The plastic injection process involves heating polymer granules, melting them, and injecting them into molds. During this process, heaters provide the high temperatures necessary for melting the plastic material.
Heaters for plastic injection can be used in the following ways:
1. Mold Heaters: Plastic injection molds take the shape of the plastic material to be melted. Heaters heat the molds, making them capable of melting, which allows the material to be injected into the mold.
2. Nozzle Heaters: Plastic injection nozzles facilitate the injection of molten plastic material into the mold. Heaters are used to heat these nozzles, aiding in the material’s flowability.
3. Cylinder Heaters: Cylinders in plastic injection machines play a critical role in melting and shaping polymer material. Heaters melt the material inside the cylinders. These heaters are typically made of special alloys that are resistant to high temperatures and can reliably operate at high temperatures. Precise temperature control is important for the quality melting and injection of plastic material, and this process can be achieved through the proper design and use of heaters.
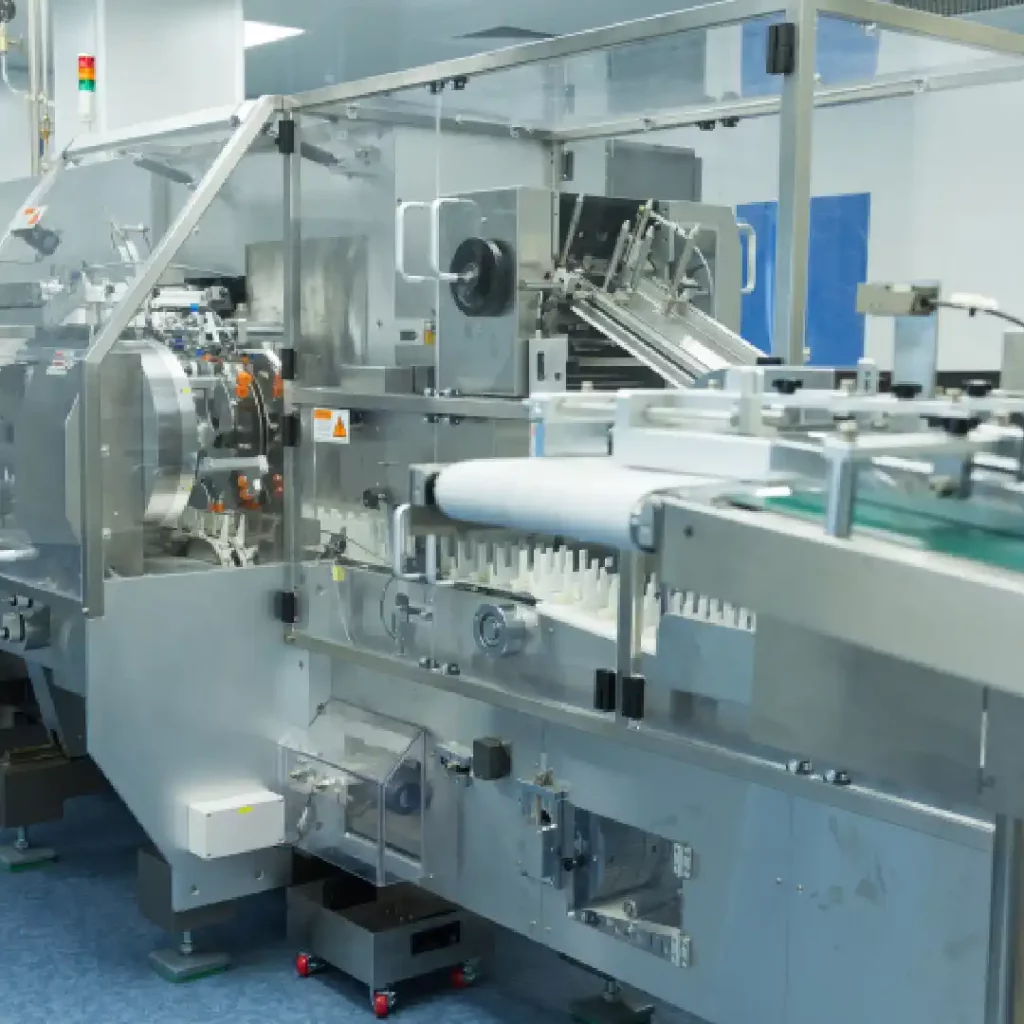
Our Products
Your Solution Partner for All Your Resistance Needs
Why Use Plastic Injection Heaters?
Heaters for plastic injection are a fundamental component for the plastic injection process and are used for several key reasons:
1. Melting Plastic Material: Heaters for plastic injection are used to melt polymer granules or plastic material. These heaters heat molds, nozzles, or cylinders to provide sufficient temperature to make the material injectable into molds.
2. Process Control and Quality: The plastic injection process is a precise operation where temperature control is critical. Heaters maintain the material within a specific temperature range to achieve the desired consistency. This ensures plastic parts are produced in the desired size, shape, and quality.
3. Productivity and Efficiency: Heaters ensure plastic injection machines operate efficiently and continuously. Rapid and consistent melting of the material can increase the speed of the production process and enhance productivity.
4. Adaptability for Various Applications: Heaters for plastic injection can be designed in various forms to accommodate different types of plastics, mold sizes, and industrial requirements. This allows for their use in various industrial applications.
5. Energy Efficiency: Well-designed heaters can maintain a specific temperature while efficiently using energy. This can lead to cost savings in energy expenses for businesses.
Heaters for plastic injection play a crucial role in the production of many plastic products. Achieving high precision, control, and efficiency requires proper design and utilization of heaters to meet the requirements of modern industrial processes. This is often essential for the successful execution of the plastic injection process.
The Importance of Plastic Injection Heating
The importance of heaters for plastic injection extends to a range of critical impacts on the plastic injection process and industrial production processes. Some significant contributions of these heaters include:
Accurate Temperature Control and Quality: Heaters for plastic injection are used to heat injection molds, nozzles, or cylinders to melt and shape plastic material. Precise temperature control ensures homogeneous melting of the plastic material and achieves the desired mold or form during the injection process, thereby enhancing product quality.
Productivity and Efficiency: Heaters increase productivity by enabling rapid and consistent melting of the material. Well-designed heaters can reduce time in the production process and allow businesses to achieve higher production rates.
Flexible Applicability: Heaters with different specifications can be designed for various plastic types, mold sizes, or industrial requirements. This enables their use in diverse industrial applications and provides flexibility in production.
Improvement in Quality Control: Temperature control is a crucial factor affecting product quality in the plastic injection process. Heaters provide stable temperature control, resulting in more consistent products and meeting quality standards.
Energy Efficiency: Well-designed heaters can maintain specific temperatures while efficiently using energy. This saves energy costs for businesses and contributes to a more environmentally sustainable production process.
Heaters for plastic injection play a significant role as a critical component in industrial production processes, influencing factors such as product quality, efficiency, and flexibility. Properly designed, high-quality heaters, when used correctly, can make significant contributions to achieving desired outcomes in the plastic injection process.
Heaters Used in Plastic Injection Sector
Heater Bands: These heaters consist of resistance wires placed on a metal strip and can be applied especially by wrapping around cylinders or molds. They can heat a large surface area and are typically available in various thicknesses and sizes.
Sealed Heaters: These heaters are coated with a special material to be more resistant to water or chemicals. This makes them more durable against moisture and various chemicals.
Cylinder Heaters: Found in cylinders used for melting and shaping plastic material. Heaters placed on the inner surface of cylinders heat the polymer material and make it fluid.
Nozzle Heaters: Used for heating plastic injection nozzles. Heaters placed inside the nozzles help the plastic material become fluid and facilitate a more controlled injection process.
Spiral Heaters: These heaters are typically inserted into pipes, which help the plastic material become fluid.
Ceramic Heaters: A type of heater with high temperature resistance, typically used in industrial applications. They can be preferred in special industrial processes and high-temperature plastic injection machines.
These types of heaters are used at various stages and in different applications in the plastic injection process. Each performs a specific task to ensure the plastic material is melted, shaped, and injected at the correct temperature.
Technical Specifications of Plastic Injection Heaters
Material and Structure: Heaters are typically made of nickel-chromium (NiCr) alloys, stainless steel, or copper-based alloys. These materials are resistant to high heat and oxidation.
Heat Resistance and Temperature Range: Heaters are usually designed to work in heating processes and can operate between 200°C and 400°C. They can withstand higher temperatures for some special applications.
Power Capacity: The power capacity of heaters is expressed in watts and indicates how much heat they can generate at a specific temperature in a given time. This is often related to the size and specifications of the heater.
Size and Dimensions: The diameter, length, and shape of heaters vary depending on the requirements of the equipment they will be used in. They can be manufactured in different diameters and sizes.
Electrical Connection and Control: Heaters typically have standard electrical connections. They can be compatible with control units, thermostats, or PID control systems. This is important for temperature control and safe operation.
Durability and Lifespan: Quality heaters are long-lasting and provide stable performance under continuous use. Depending on the environment they are used in, they can be resistant to chemicals, shocks, and high temperatures.
Application Area and Special Requirements: Some heaters can be coated with special coatings and designed for industrial applications requiring special chemical resistance.
The technical specifications of heaters vary depending on the standards specified by manufacturers, industrial usage purposes, and requirements. These features are critical for the heating process to occur correctly and efficiently in the plastic injection process.