Mold Manufacturing Heaters
Why are Heaters Used in Mold Manufacturing?
Heaters for mold manufacturing are essential components used to heat and maintain the desired temperature of industrial mold and press machines. These heaters are utilized to provide the necessary temperature for shaping and processing materials used in mold manufacturing. Here are the reasons for using heaters in mold manufacturing:
Material Shaping and Processing: Heaters for mold manufacturing are used in the shaping and processing of materials such as metal or plastic. These heaters maintain specific temperature values required for materials to be shaped and processed.
Fast Heating and Cooling: Heaters for mold manufacturing possess the capability of rapid heating and cooling. This facilitates more efficient and faster production processes.
Temperature Control: Maintaining the desired temperature of materials within molds is critical in mold manufacturing processes. Heaters ensure this temperature control, allowing materials inside the mold to attain the desired properties.
Energy Efficiency: The rapid heating and cooling capabilities of heaters increase energy efficiency. This reduces energy costs in mold manufacturing and makes the processes more sustainable.
Variety of Uses in Production Processes: Heaters for mold manufacturing can be used in various applications for different types of materials and production processes. This versatility accommodates different industries and application requirements.
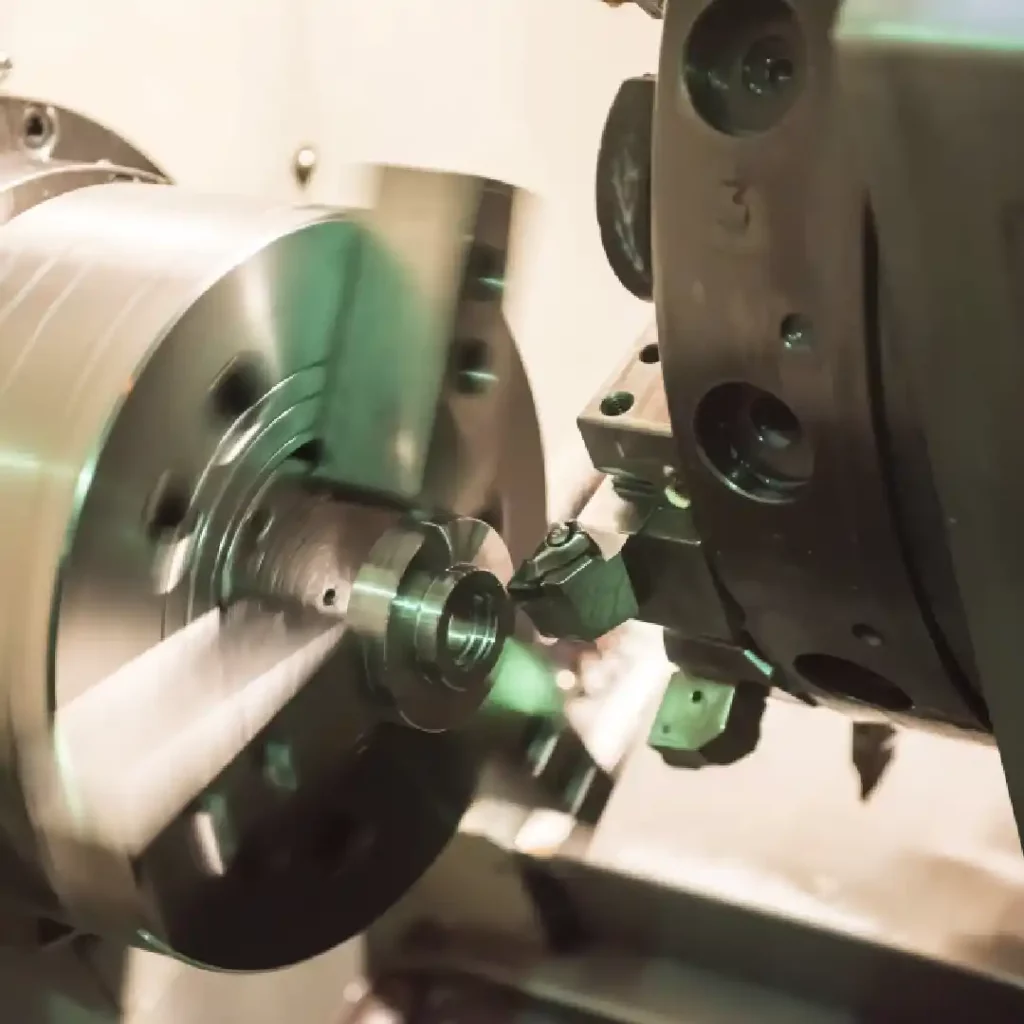
Our Products
Your Solution Partner for All Your Resistance Needs
Importance of Heaters in Mold Manufacturing
Heaters for mold manufacturing play a crucial role in industrial processes, controlling the temperature of mold press machines and shaping and processing materials. The importance of these heaters can be summarized as follows:
Temperature Control: Heater for mold manufacturing precisely controls the temperature of mold press machines, ensuring materials are heated and processed at the correct temperature.
Material Shaping: Heaters are used in the process of shaping materials such as metal or plastic in molds. Materials are held at specific temperatures to be shaped and take on the characteristics of the mold.
Fast Heating and Cooling: Heaters for mold manufacturing have the ability for rapid heating and cooling, speeding up production processes, leading to shorter production times and increased efficiency.
Product Quality: Proper temperature control enhances product quality. Uniform heating and shaping of the material result in products with desired characteristics.
Energy Efficiency: Heater efficiency reduces energy costs in the process. Rapid heating and cooling ensure effective energy usage.
Longevity: Designed to withstand industrial conditions, mold manufacturing heaters offer longevity and low maintenance requirements.
Various Applications: Heaters can be used in various application areas for processing and shaping different materials and industrial applications, providing solutions tailored to various industry needs.
Sustainable Production: Mold manufacturing heaters promote sustainable production with optimized processes in energy efficiency and material usage.
High Temperature Resistance: Heaters designed to withstand high temperatures provide reliable performance within the required temperature ranges for industrial processes.
Heaters for mold manufacturing increase production efficiency by providing reliability, precision, and effective temperature control in industrial production processes. These heaters stand out as a critical component to improve the quality of mold manufacturing, reduce energy costs, and make processes more sustainable.
Technical Specifications of Heaters Used in Mold Manufacturing
The technical specifications of heaters used in the mold manufacturing sector may vary depending on specific application requirements, but generally include the following features:
Material and Construction: Nickel-chromium alloys or special alloys capable of withstanding high temperatures are used as heater materials. The construction is designed to be long-lasting and durable.
Nominal Power Capacity: The nominal power capacity of heaters determines the amount of energy required to process materials at a specific temperature. This is determined according to the heating requirements in the production process.
Nominal Voltage: Heaters are designed to operate at a specific nominal voltage. This should comply with industry standards and the electrical system of the equipment being used.
Temperature Range: The operating temperature range of heaters should be suitable for the temperature values required to process materials. This range may cover a wide spectrum of temperatures as different materials and processing requirements vary.
Resistance Value: The resistance value of the heater is determined to provide the desired power level at a specific temperature. Resistance value is important for controlling the effect of the heater on the material.
Rapid Heating and Cooling Capability: Rapid heating and cooling are critical for efficient production processes in mold manufacturing. Heaters with these capabilities optimize production processes.
Longevity and Durability: Heaters designed to withstand industrial conditions should demonstrate resilience to vibrations, shocks, and high temperatures. Their longevity reduces maintenance costs.
Mounting and Integration Capability: Heaters should be easily mountable and integrable with mold press machines. They should offer various mounting options and adaptation capabilities.
Protection Systems: Heaters can be equipped with protection systems against overheating or other potential issues. This enhances safety and helps prolong the equipment’s lifespan.
These features represent the general technical specifications of heaters that can be effectively utilized in mold manufacturing processes.
Things to Consider When Choosing Mold Manufacturing Heaters
When selecting heaters for mold manufacturing, it’s important to pay attention to various factors to ensure the right equipment is chosen. Here are the considerations to keep in mind when selecting heaters for mold manufacturing:
Application Requirements: Firstly, determine the application requirements such as the type of material being processed and details of the processing processes. This will be crucial for ensuring proper temperature control and power capacity.
Temperature Range: The operating temperature range of the heater should be suitable for the properties of the material being processed. Consider the temperature values required by the process.
Power Capacity and Voltage: The nominal power capacity and voltage of the heater should match the processing requirements. This ensures proper processing of the material at the correct temperature.
Heating and Cooling Rate: Mold manufacturing processes often require rapid heating and cooling. Check if the heater is capable of meeting these speeds.
Durability and Material Selection: The material used in the construction of the heater affects its durability and longevity. Prefer materials that can withstand high temperatures and resist wear.
Ease of Mounting and Integration: The heater should be easy to mount and integrate. Compatibility with relevant equipment and machinery is important.
Protection and Safety Features: Heaters equipped with protection systems against issues like overheating and overcurrent are important for safety.
Energy Efficiency: Energy efficiency can reduce operating costs. Check if the heater has features aimed at energy savings.
Ease of Maintenance and Cleaning: The heater should be easy to maintain and clean. This is important for longevity and operational efficiency.
Regulation and Control Systems: It’s important for the heater to have appropriate control systems for temperature regulation. These systems are used to achieve desired temperature profiles.
Cost Factors: Lastly, consider the cost of the heater and long-term cost-effectiveness. Conduct a cost analysis based on performance and features.
By considering these factors, the selection of heaters for mold manufacturing can be done more accurately and efficiently.
Nozzle and Spiral Heaters Used in Mold Manufacturing Industry
Heater Elements Used in Mold Manufacturing Sector:
Nozzle Heaters:
Purpose and Usage: Nozzle heaters are commonly used in injection molding machines. In these machines, they facilitate the passage of molten plastic material through the nozzle to the mold injection point. Nozzle heaters are employed to control the flow of material at this point and maintain the temperature at the desired level.
Technical Specifications: They must be capable of operating at high temperatures and have rapid heating and cooling capabilities. They can be made of stainless steel or special alloys.
Installation and Integration: They should be mounted in accordance with the design of the injection machine.
Spiral Heaters:
Purpose and Usage: Spiral heaters, commonly known as spray heaters, typically facilitate the spraying and distribution of material inside the mold. This aids in shaping the material uniformly and easing its pouring into the mold.
Technical Specifications: Ability to operate at high temperatures is crucial. They need to be capable of controlled heating during the material spraying process.
Installation and Integration: They should be integrated into the mold design appropriately. Spray nozzles and heaters must be carefully positioned to ensure even distribution of the material.
These types of heaters ensure that the materials used in mold manufacturing are kept at the correct temperature for shaping. While nozzle heaters focus on temperature control in injection molding machines, spray heaters ensure the homogeneous distribution of material within the mold. These heaters play a significant role in optimizing production processes, enhancing quality, and ensuring energy efficiency.