Heating and Cooling Heaters
Material Processing and Manufacturing: Many manufacturing processes require specific temperatures to be maintained. Heater elements are used in material processing to facilitate tasks such as shaping, drying, or hardening of materials.
Heating and Cooling Equipment: Industrial ovens, boilers, water heaters, and cooling systems incorporate heater elements. These equipment often contain specially designed heaters to ensure energy efficiency and precise temperature control.
Chemical Reactions: Certain chemical reactions need to occur at specific temperatures. Heater elements are used to maintain the desired temperature conditions in chemical processes.
Hot Water and Steam Generation: Heaters used in boilers or water heaters manage the production of hot water and steam. This is a common application in industrial facilities and heating systems.
Automotive and Electronics Manufacturing: Temperature control is critical in automotive and electronics industries, particularly in soldering processes and other delicate manufacturing procedures. Heater elements are utilized in these applications.
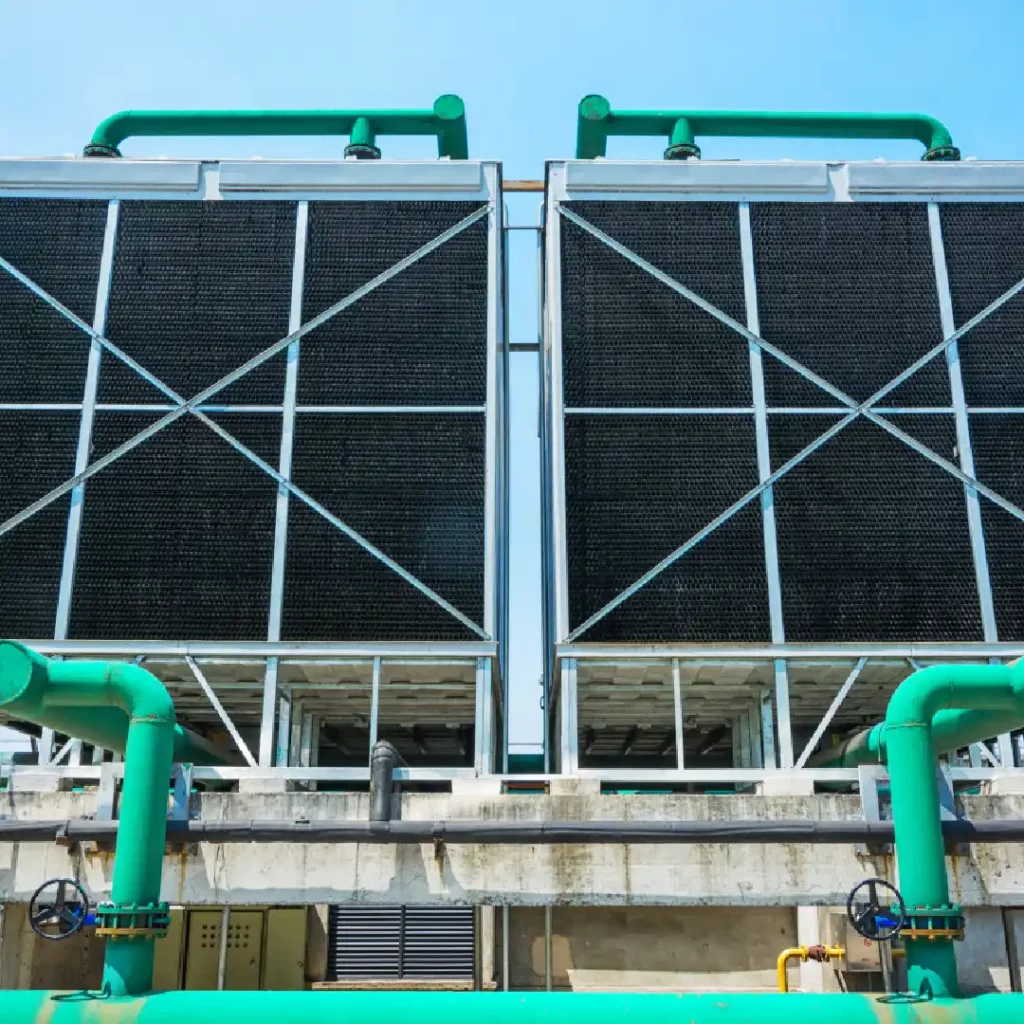
Our Products
Your Solution Partner for All Your Resistance Needs
The Importance of Heating and Cooling Heaters
Heaters play a significant role in many industrial applications and offer a range of advantages. Here are some key reasons to understand the importance of heating and cooling heaters:
Temperature Control: Heating and cooling heaters are used to ensure temperature control in industrial processes. This helps maintain desired temperature conditions in manufacturing processes and enhances product quality.
Energy Efficiency: Heater elements provide efficient heat production by directly converting energy into heat. This can reduce energy costs and lower operating expenses.
Fast Heating and Cooling: Heaters are ideal for equipment that can quickly reach a specific temperature and control temperature rapidly. This can shorten process times and increase productivity.
Product Quality and Reduced Inconsistencies: Heating and cooling heaters are used in industrial production processes to ensure product quality and reduce product inconsistencies. Maintaining production at a specific temperature helps uphold quality standards.
Customizability: Heaters can be designed to meet different requirements for various applications and industries, providing custom solutions. This caters to various industrial needs and processes.
Longevity and Durability: Heaters made from high-quality materials are long-lasting and durable. This reduces maintenance costs and ensures equipment operates smoothly for an extended period.
Precise Temperature Control: Precise temperature control is critical in some industrial applications. Heaters can minimize temperature fluctuations and maintain desired temperature levels.
Safety: Heating and cooling heaters are important for safety as well. Properly designed and regulated heaters prevent overheating, overcooling, or other safety risks, ensuring the safety of workers and equipment.
Given the significant role heating and cooling heaters play in many industrial processes and applications, properly selected and regulated heaters can enhance efficiency and optimize product quality for businesses.
Technical Specifications of Heaters Used in Heating and Cooling Sector
The technical specifications of heaters used in the heating and cooling industry can vary depending on their intended use and applications. However, generally, some common technical features of such heaters may include:
Material: Heaters are typically made from heat-resistant alloys such as stainless steel, nickel-chromium alloys, etc.
Durability: Heating and cooling heaters should generally be long-lasting and durable, achieved through quality materials and manufacturing processes.
Power Capacity: The power capacity of heaters indicates the amount of heat they can generate within a specific period, varying based on usage and application needs.
Voltage and Current Ratings: The operating voltage and current ratings of heaters determine their electrical characteristics, selected according to specific application requirements.
Temperature Tolerance: Heaters typically operate safely within a certain temperature range, which varies depending on application needs and environmental conditions.
Mounting and Connection: Heater mounting and connection should be compatible with the equipment or system they will be used with, offering various mounting types and connection options.
Insulation: Heating and cooling heaters are usually covered with insulation material capable of withstanding high temperatures, important for safety and performance.
Size and Geometry: Heater size and geometry may vary based on mounting location and application requirements, with measurements such as length, width, and diameter being crucial.
Regulation and Control: Some heaters may have regulation and control features to maintain or adjust a specific temperature level.
Safety Standards and Approvals: Heaters should comply with specific safety standards and hold necessary approvals for safety and reliability.
Considering these technical specifications is crucial for ensuring the safe, effective, and efficient operation of heating and cooling heaters. Since each application has its unique requirements, correctly identifying these features is essential when selecting heaters.
Considerations When Choosing Heating and Cooling
The selection of heating and cooling systems is a crucial decision in industrial and commercial applications. Choosing the right system is critical for energy efficiency, cost savings, and system performance. Here are some important factors to consider when selecting heating and cooling systems:
Application and Industry Requirements: Firstly, it’s important to determine the heating and cooling needs for a particular application or industry. Different industries may have different requirements.
Needs Analysis: Before selecting a system, a needs analysis should be conducted. Requirements should include equipment capacity, temperature requirements, energy efficiency, and other specific needs.
Energy Efficiency: Energy efficiency is important for long-term cost savings. Heating and cooling systems with high energy efficiency should be selected.
Environmental Factors: Environmental impacts and sustainability should be considered. Systems with a low carbon footprint may be preferred.
Cost Analysis: System costs, including installation, maintenance, and operating costs, should be taken into account. A system that provides the most economical solution in the long term should be selected.
System Integration: When selecting a heating and cooling system that meets the requirements, it’s important to check if it is compatible with existing infrastructure and equipment. System integration is important for efficiency and compatibility.
System Reliability: Reliability is a critical factor in heating and cooling systems. Reliable systems are important for business continuity and production continuity.
Ease of Maintenance: The selected system should be easily accessible and manageable for regular maintenance and repair operations. Maintenance ease is critical for maintaining system performance over the long term.
Regulation and Control: A good heating and cooling system should be able to effectively control parameters such as temperature, pressure, and others. Automation and control systems can enhance system efficiency.
Spare Parts and Service Support: Sufficient spare parts and service support should be available with the selected system. This is important for providing quick solutions to system failures.
Legal and Safety Standards: Compliance with relevant legal and safety standards is important. This ensures that business processes are conducted in accordance with laws.
Considering these factors when selecting heating and cooling systems can help ensure system performance, energy efficiency, and long-term cost savings.