Boiler Manufacturing Heaters
Boiler manufacturing involves the fabrication of a plumbing and equipment system used for the production of hot water or steam for energy generation, heating, process heat, and industrial applications. There are several reasons why boilers are used in many industrial and commercial applications:
Heat Generation: Boilers produce heat through the combustion of fuels or the use of electrical energy. This heat can be used for the production of hot water or steam. While hot water can be used in heating systems, process water heating, and various industrial applications, steam energy production can be utilized in industrial processes, electricity generation, or heating systems.
Energy Generation: Boilers are used in the production of various types of energy. Particularly, thermal energy production involves the generation of electricity through steam turbines or generators.
Hot Water Supply: Boilers are used for supplying hot water in buildings. This includes providing hot water for bathing, kitchen use, or general purposes.
Industrial Applications: Boilers are utilized in industries such as petrochemicals, food and beverage, textiles, paper production, and many others. In these sectors, boilers can be used for providing process heat, energy generation, and various stages of production.
Heating Systems: Boilers are employed in heating systems for buildings. By circulating hot water or steam through radiators or underfloor heating systems, boilers ensure the heating of the indoor environment.
Boilers should be designed and operated with consideration for energy efficiency, reliability, and environmental impacts. This is important for ensuring sustainable energy production and reliable performance in industrial applications.
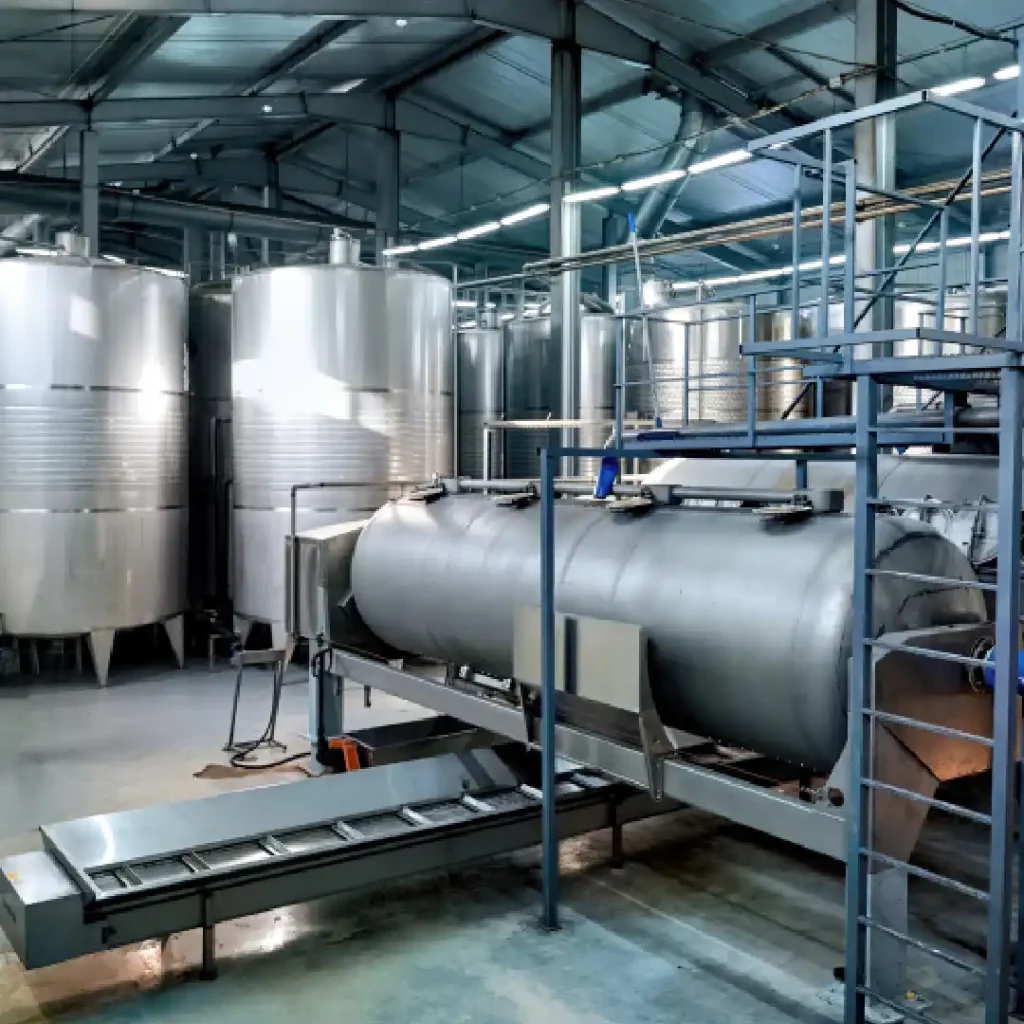
Our Products
Your Solution Partner for All Your Resistance Needs
Importance of Boiler Manufacturing Heating
Boiler manufacturing heaters are critical components used for heat generation or hot water supply in boiler systems. There are several important reasons for using these heaters:
Heat Generation: Boiler manufacturing heaters convert electrical energy into heat by heating water or fluid to produce steam. This steam can be used in energy production, heating systems, or industrial processes.
Energy Efficiency: Heaters used in boiler systems may have designs aimed at increasing energy efficiency. High-efficiency heaters can produce more heat with less energy consumption, resulting in energy savings.
Quick Response: Electric heaters can generate heat quickly, allowing boiler systems to heat up rapidly and reach desired temperatures quickly.
Controllability: Electric heaters can be controlled with precision, enhancing the boiler system’s compliance with desired conditions by controlling temperature, pressure, and other parameters.
Low Maintenance Requirement: Electric heaters generally require low maintenance. They contain fewer parts compared to other heating methods and have a lower risk of mechanical wear, reducing maintenance costs.
Environmental Friendliness: Electric energy can be a clean energy source, and electric heaters used in boiler manufacturing can reduce adverse effects on the environment. They may have a lower carbon footprint compared to other energy sources.
Flexibility: Electric heaters can be manufactured in various sizes and designs, providing compatibility with different boiler systems and applications.
Boiler manufacturing heaters play a significant role in energy production and industrial heating systems. Properly designed and used heaters ensure the reliable and efficient operation of boiler systems.
Technical Specifications of Heaters Used in Boiler Manufacturing Sector
The technical specifications of heaters used in boiler manufacturing can vary depending on specific applications and requirements. However, generally, some common technical specifications of such heaters may include:
Nominal Power (Watt): The nominal power of the heater indicates its ability to operate at a certain temperature and a specific electric current. This feature is important to evaluate whether the heater is suitable for a particular application.
Nominal Voltage (Volt): The nominal voltage of the heater indicates the required electrical voltage for safe and effective operation in a specific application.
Resistance Value (Ohm): The resistance value of the heater represents its resistance to electric current at a certain temperature. This value is important to determine the compatibility of the heater with application requirements.
Temperature Coefficient: The temperature coefficient of the heater indicates how sensitive the resistance value is to temperature changes. This is particularly important in applications requiring temperature control.
Insulation Material: The insulation material on the heater affects its resistance to environmental conditions, chemicals, and other external factors. Different insulation materials may be preferred for different applications.
Dimensions and Design: The dimensions and design of the heater are determined to ensure compatibility with the type, size, and application requirements of the boiler. This is important for ease of installation and mechanical durability.
Protection Class and Standards: Heaters are generally required to comply with specific protection classes (IP ratings) and industry standards. This indicates their resistance to various environmental conditions depending on the application.
Cable Connections: Having appropriate cable connections is important for integrating the heater with the boiler system.
Corrosion Resistance: Heaters used in boiler systems should be resistant to corrosion to ensure long-term reliability and performance.
The proper selection of heaters used in boiler manufacturing ensures the efficient and reliable operation of the boiler. Therefore, it is important to select heaters with appropriate technical specifications considering specific application requirements.
Things to Consider When Choosing Boiler Manufacturing
Making the right choices in boiler manufacturing is critical for energy efficiency, reliability, and a long-lasting boiler system. Here are some important factors to consider in boiler manufacturing selection:
Application Requirements: The application and industry type where the boiler will be used must be determined. Different industry sectors may have different heating needs.
Operating Pressure and Temperature: The operating pressure and temperature of the boiler should be determined, and it should be verified whether the selected boiler is suitable for these conditions.
Fuel Type: The type of fuel the boiler will use must be determined (e.g., natural gas, fuel oil, coal, biomass). Fuel selection should include cost, availability, and environmental factors.
Energy Efficiency: The energy efficiency of the boiler should be evaluated. High-efficiency boilers can reduce energy costs and minimize environmental impacts.
Boiler Size and Capacity: The size and heat production capacity of the boiler must be suitable for application requirements. The boiler should meet the specified heating demand.
Material and Manufacturing Quality: The quality of materials used in boiler manufacturing affects durability and longevity. High-quality materials and a good manufacturing process can increase the reliability of the boiler.
Emission Control: Compliance with various local and national emission standards should be assessed. This is important to ensure compliance with environmental regulations.
Ease of Maintenance: The boiler should be easy to maintain and repair. This can reduce operating costs and ensure the boiler operates effectively.
Control and Automation Systems: Modern control and automation systems should be used for the boiler to operate efficiently. This is important for monitoring and optimizing boiler performance.
Safety Standards: Compliance with safety standards for the boiler should be evaluated. Safe operation and use of the boiler ensure worker safety and facility security.
Operating Costs: The cost of the boiler should include not only the purchase cost but also operating, maintenance, and energy costs. A total cost of ownership assessment should be conducted.
These factors are important considerations in boiler selection. Making the right choices in the boiler manufacturing sector is critical for increasing energy efficiency, reducing costs, and ensuring reliable operation.
Head Tube Heater Used in Boiler Manufacturing Sector
Flanged tube heaters used in the boiler manufacturing sector are employed to heat liquid or gas in boiler systems. These heaters are units placed inside tubes that produce heat using electrical energy. Here are some features of flanged tube heaters:
Material: Flanged tube heaters are typically made of corrosion-resistant materials such as stainless steel or incoloy. These materials can withstand high temperature and pressure conditions and provide reliable performance in boiler systems.
Resistance Value: The resistance value of the heater is selected according to the specifications of the boiler system. The resistance value indicates the electrical resistance of the heater and determines its heat-producing capacity.
Power Capacity: The power capacity of flanged tube heaters determines their ability to operate within a specific temperature range. This is important for providing the heating capacity required by the boiler.
Size and Design: The size and design of flanged tube heaters are determined to fit the space where they will be installed in the boiler system. This is important for ease of installation and mechanical durability.
Protection Class and Standards: Flanged tube heaters generally need to comply with specific protection classes (IP ratings) and industry standards. This indicates their resistance to various environmental conditions depending on the application area.
Temperature Control Elements: Some designs of flanged tube heaters may include temperature control elements. These elements measure the temperature of the liquid or gas in the boiler system and adjust the heater’s operating parameters accordingly to reach the desired temperature.
Ease of Installation: The design of flanged tube heaters should facilitate ease of installation and maintenance. This is important for the operation and maintenance of the boiler system.
Flanged tube heaters can enhance energy efficiency and provide the desired temperature conditions in boiler systems for heating processes. These heaters can be used in various applications ranging from industrial facilities to commercial buildings.